It was a dreary afternoon on a Saturday in late October, and the reception-area lights at NYU Langone’s imaging clinic in Gramercy Park had already been turned off. From the street, the place looked empty. But inside, past waiting rooms, scanner bays, and offices, a brightly lit laboratory buzzed with dozens of people who, running on much caffeine and little sleep, worked to meet the approaching evening’s deadline in a quest that had brought them together a few days before: to build a low-field MRI scanner and use it to peer inside an opaque object.
The challenge, called “MRI4ALL” and hosted by NYU Langone, attracted more than 50 volunteers who formed five teams that would create and integrate the hardware and software components of an MRI machine: magnets, gradients, a radio frequency coil, scanner controls, and user interface. The teams were led by MRI experts from the Center for Biomedical Imaging and the Center for Advanced Imaging Innovation and Research at NYU Langone, the Antinoula A. Martinos Center for Biomedical Imaging at Massachusetts General Hospital, and the Biomedical Imaging and Bioengineering Institute at Icahn School of Medicine at Mount Sinai.
Inside the low-field laboratory at Gramercy Park, Jason Stockmann, PhD, assistant professor of radiology at Harvard Medical School and researcher at the Martinos Center, stood amid a group of people clustered around a utility cart laden with the fruit of the week’s labors: a white cylinder, about the size of a mini fridge, ringed with purple fins and connected by cables, wires, and piping to boxy components on the cart’s lower tiers. It was a miniature MRI by its looks, but not yet by function.
“What’s preventing us from getting an FID at this point?” Dr. Stockmann asked, using a shorthand for free induction decay, one of the most fundamental types of signal in nuclear magnetic resonance. “We just need a coil holder—that’s about an hour and a half away,” came an answer. “We can take a spin echo even without the RF shield,” came another. “Something’s burning,” said one participant, apparently unaware that the thin wisps of smoke wafting through the air came from a soldering iron used to affix gradient filters to a metal plate at the back of the cart.
Nearby, Leeor Alon, PhD, assistant professor of radiology at NYU Langone, scientist at the Center for Advanced Imaging Innovation and Research, affiliated faculty member at the Tech4Health Institute, and one of the hackathon’s lead organizers, tilted back in a chair with his feet up on a desk and tapped at a laptop displaying computer models of the MRI magnet, generated by software he wrote specifically for this purpose. Dr. Alon had been incubating an idea for an event like this for years. In the summer of 2023, he obtained about $10,000 in internal funding to hold the event and began recruiting team leaders.
Even though there were still several hours to go and the scanner had yet to produce images, Dr. Alon’s buoyant mood showed that from his perspective the event had already been a huge success. MRI experts, students, and technology aficionados from more than a dozen research institutions came together to create a sophisticated imaging instrument and shared an experience that many found both demanding and satisfying. “The people have been amazing,” he said. “It’s so cool to see there’s so much passion that goes into this field.”
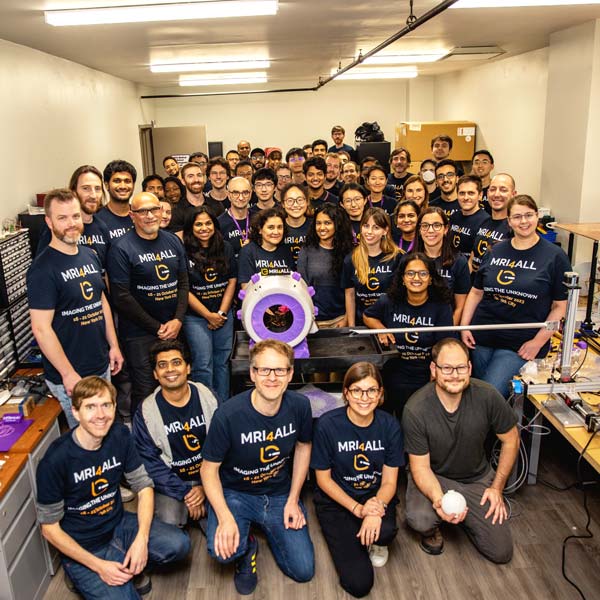
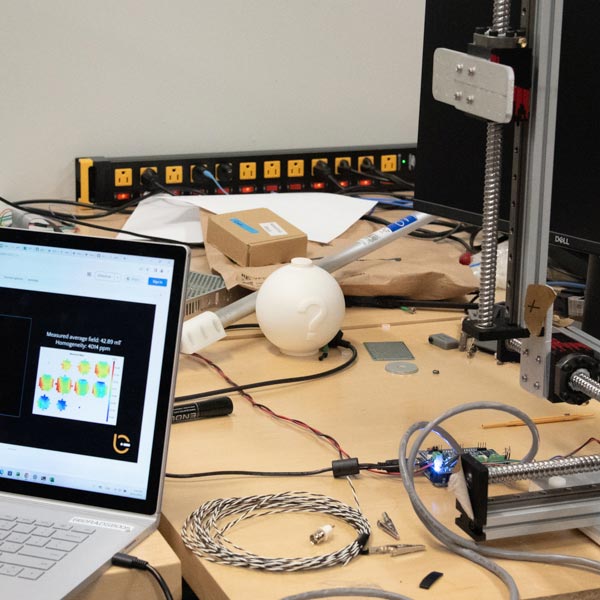
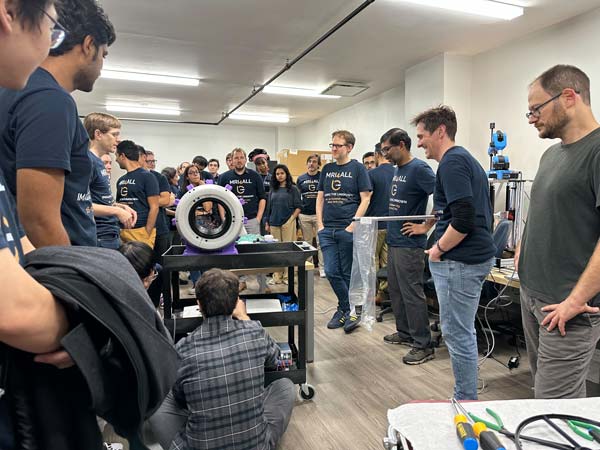
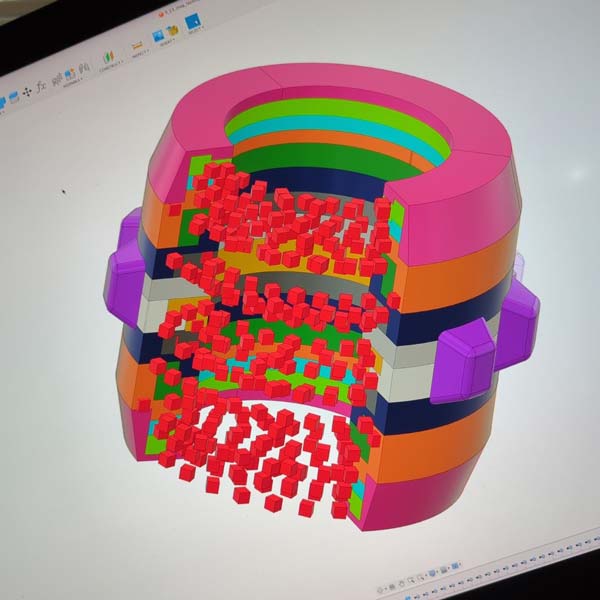
Hands-On Experience
When the hackathon participants reported to their locations on the preceding Monday, they weren’t exactly starting from the proverbial drawing board. The teams had worked together remotely for several weeks on computer simulations and computer-aided design models of the system. Plastic elements that would give the scanner its shape had been drafted and 3D-printed in advance after “lots of testing for materials to make sure that we had the polycarbonates that worked,” said Vito Ciancia, the hackathon’s lead of 3D fabrication and senior additive manufacturing engineer at New York University’s LaGuardia Studio, an end-to-end 3D manufacturing facility. But apart form the virtual blueprints and the plastic partials, there wasn’t much else.
The magnet group began the week by unpacking one thousand magnetic blocks, each about the size of a six-sided die, marking their polarity, and spreading them far enough apart to prevent clumping. “Then we’d just grab them and put them into the 3D-printed rings,” said Clarissa Cooley, PhD, assistant professor in radiology at Harvard Medical School and researcher at the Martinos Center, who led the team. Bolted together, the rings brought 990 individual magnets into a cylindrical arrangement that intensified the field on the inside of the bore (known as a Halbach array). It was a promising outcome for a day’s work.
“But then we took it all apart,” said Dr. Cooley. Some rings didn’t sit flush against others, and a map of the magnet’s field—made with a mapping robot also built by the team—revealed an unexpected distortion. “We assumed that the variation was coming from the gap,” said Dr. Cooley. So the team came up with a new assembly process that involved epoxying each ring, clamping it down to the others, and leaving the whole stack to cure. All this pushed the magnet completion to from day one to day three.
Meanwhile, the gradient team headed by Dr. Stockmann labored to wind yards of wire onto three intricately grooved 3D-printed cylinders that, once nested inside each other and slotted into the magnet’s bore, would allow the scanner to encode spacial information. “In the beginning, it was really difficult,” said Anja Samardzija, third-year doctoral student of biomedical engineering at Yale University. Together with two teammates, she “spent five hours just winding half of one of the gradients—that was the first day.”
For Samardzija, the hands-on experience was a part of the attraction. “My research is low-field MRI, so it’s kind of perfectly aligned,” she said. Interested in implementing her own gradients, she saw the hackathon as an opportunity to work with some of the foremost experts in hardware. The team eventually used clamps to speed up the coiling of x, y, and z axis gradients, completing the assembly by day three. “By the end, we became pros at it,” she said.
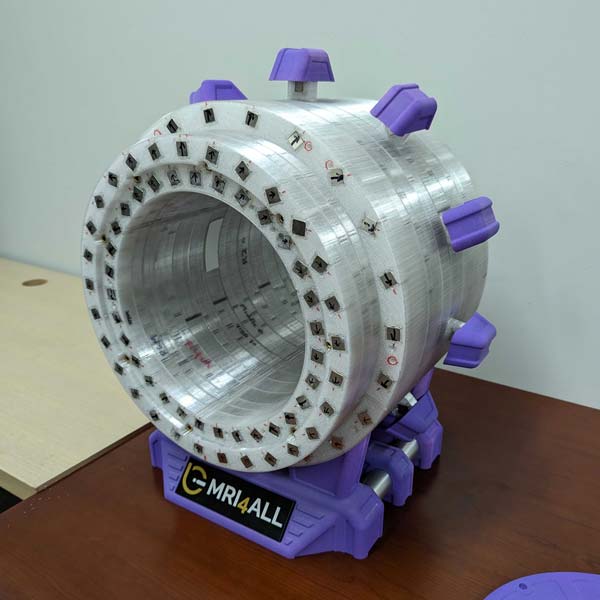
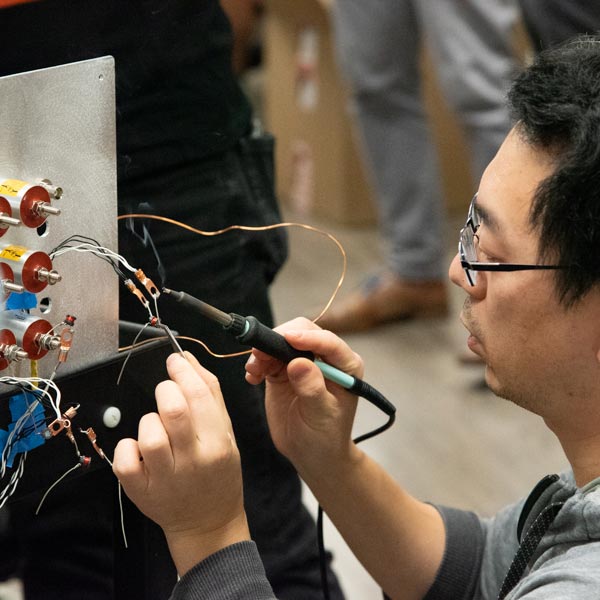
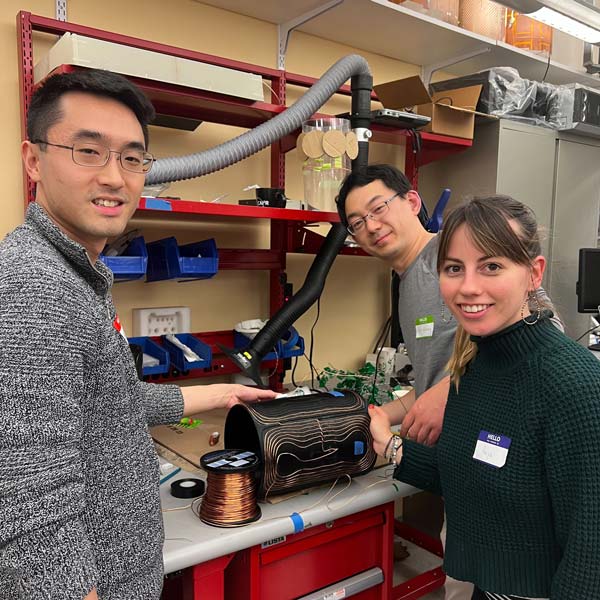
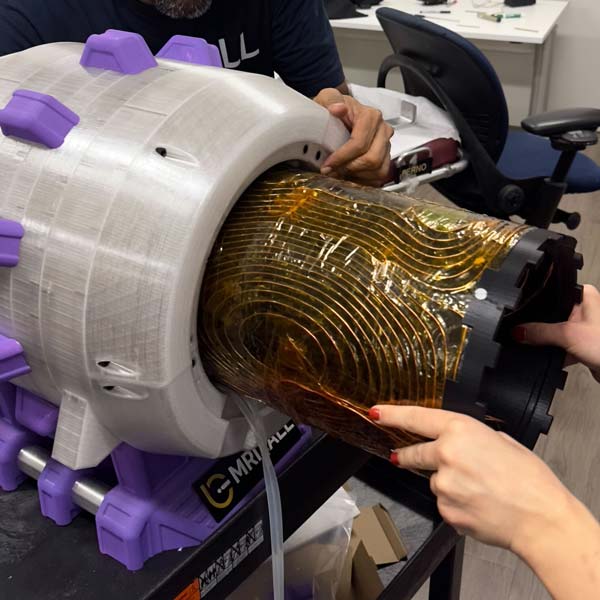
They Call It a System for a Reason
MRI scanners and their components are built through a deliberate, iterative process because every part affects the physics of the whole. The hackathon’s compressed timeline forced the teams to work with incomplete information and adapt to the system’s properties as these emerged from real-time measurements.
The field variation observed by the magnet team (some of which persisted even after reassembly) prompted the researchers to add passive shims in addition to an already planned active shim. They would have to fit three gradient coils, two types of shims, an RF shield, and a transmit/receive RF coil inside the magnet while leaving enough room to accommodate the hackathon phantom. “It’s like a nesting doll,” said Dr. Alon, but with extra dimensions. For example, the gradients and the active shim produce heat, which can cause “drift.”
“With passive magnets, the field drifts significantly when you heat or cool the temperature, and you have to be really careful to design something that’s useful but is also not going to change your frequency,” said Charlotte Sappo, PhD, postdoctoral fellow at Vanderbilt University and member of the hackathon RF team.
To guard against drift, the magnet team built an active cooling system that pumps water through a densely folded hose sandwiched between the Halbach array and the gradient coils. As things got tight inside the bore, the RF team had to scrap its first transmit/receive coil and build a new, smaller one in order to place it further from the RF shield. Having these elements too close “cancels out too much of the field … reduces inductance too much, and that reduces sensitivity,” explained Dr. Stockmann. “Even a couple of centimeters can make a big difference.”
“Working around a system the parameters of which you’re not sure of is difficult,” said Dr. Sappo. She joined the hackathon “just to get creative, to bring some expertise but also gain something new,” she said. “It’s been amazing, it’s been extremely collaborative.”
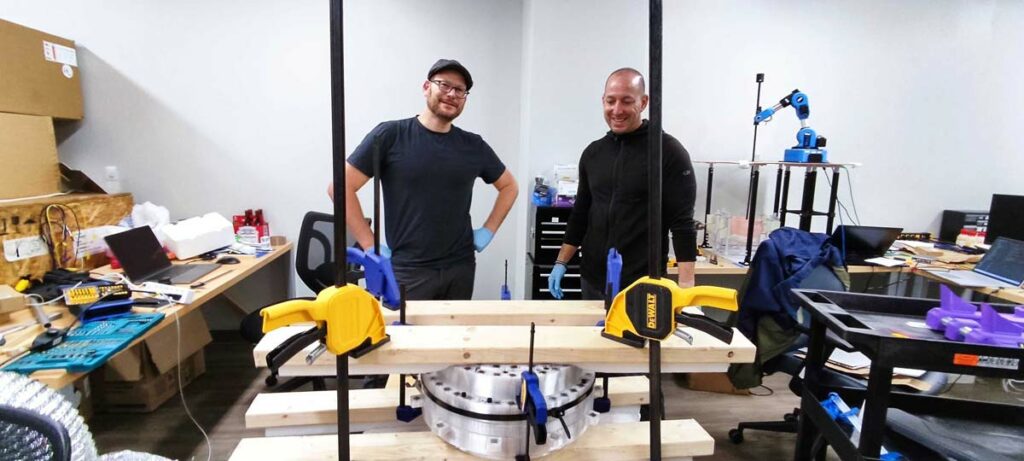
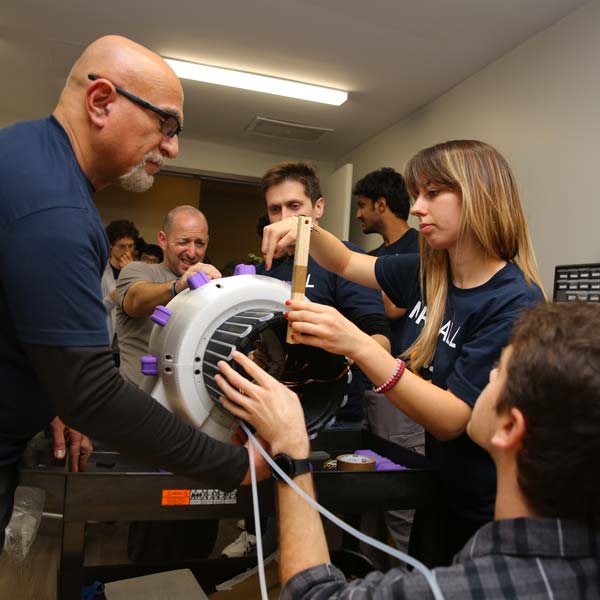
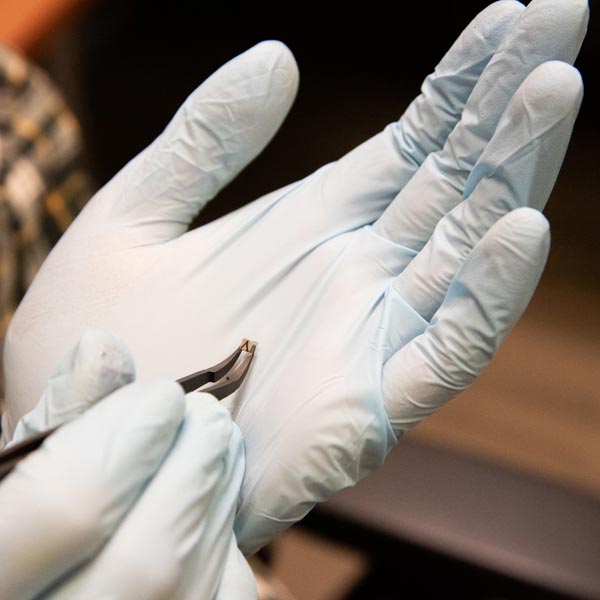
‘Crazy’
On Saturday afternoon, some four hours before the hackathon’s 8:00 p.m. deadline, a handful of participants worked at NYU Langone’s RF laboratory in Murray Hill, about a mile away from Gramercy Park. They were finalizing an active muti-coil shim array, a component that would complement the passive shim to make the scanner’s magnetic field more uniform—a novelty in a low-field system.
“It’s the only one I know,” said Sebastian Theilenberg, PhD, associate research scientist at Columbia University who specializes in active shim arrays, typically built for much stronger and larger scanners. “Active shim arrays were originally conceived to get the best possible homogeneity,” he said. The design, based on the previously simulated magnet properties, was revised several times during the week based on field measurements from the magnet team “to make sure that our input is as close to what’s actually happening as possible.” The assembly began on Friday and took at least five people. “It’s very much manual labor, and we have 30 channels, so everything you have to do 30 times; some things you have to do 60 times,” Dr. Theilenberg said. “Normally it takes us months to design and build these systems.”
Nearby, Bernard Gruber, PhD, coil engineer from Austria and expert in massively parallel coil arrays, chatted about the hackathon experience with Ryan Brown, PhD, associate professor at NYU Langone and co-leader of the RF team (the team’s other co-leader was George Verghese, research engineer at NYU Langone).
“There was space to transfer knowledge to students, even in such a tight timeframe,” Dr. Gruber said. “That was completely surprising to me.” He added that he considered a student anyone who doesn’t have expertise in the task at hand, regardless of title or credentials.
Dr. Brown nodded. “On Monday, I was exhausted answering questions, and on Tuesday … everyone was just independently working,” he said. “That was really cool to see.”
Dr. Theilenberg said that participants shared knowledge “in all directions.” He particularly appreciated “all the little tricks people learn over time and that take you years to come up with, the stuff that never ends up in a paper. . . . That’s what’s really valuable—do the work together with somebody with different experience and combine that.”
Dr. Gruber, co-founder of an Austria-based MRI startup called BARNLabs, joined the hackathon after visiting Cambridge, MA, as part of a program for entrepreneurs run by the Austrian Trade Commission. “Building a scanner architecture mostly from scratch, even assembling everything within a week, is crazy,” he said with palpable enthusiasm. “It’s less than a week, right?”
A few minutes later, the RF lab contingent took the active shim and a handful of other components, piled into a cab, and headed toward Gramercy Park where the back-of-the-clinic low-field laboratory swelled with hackathon participants during the final push to integrate parts and software.
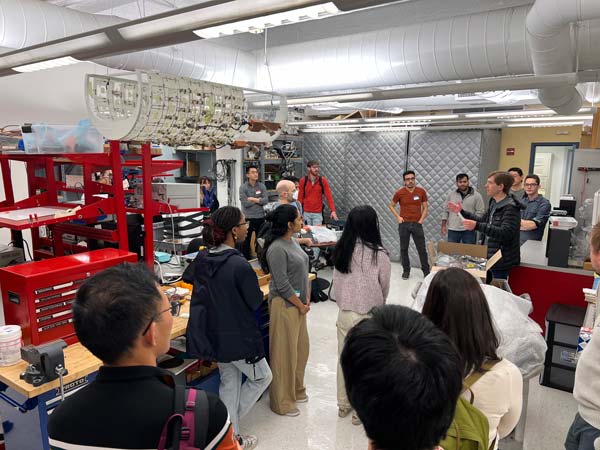
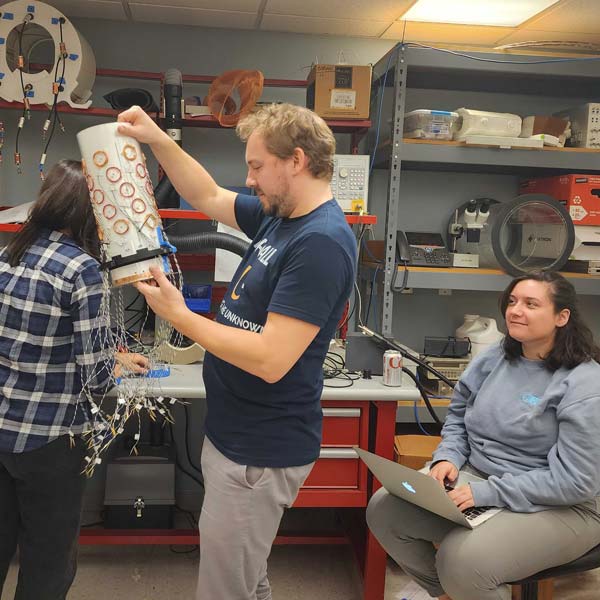
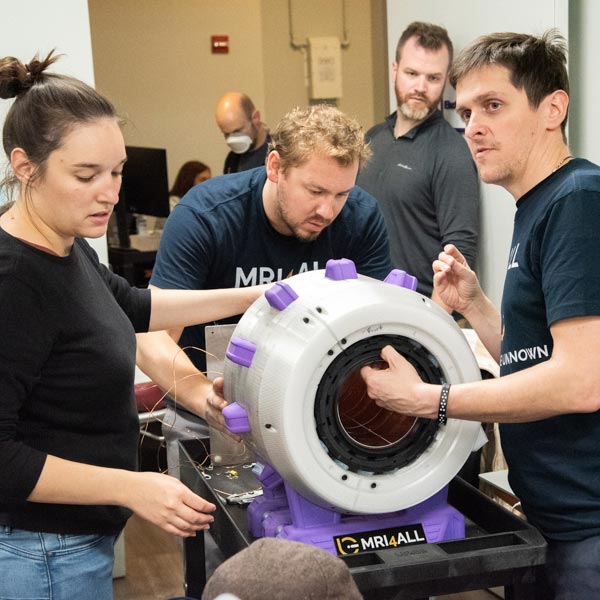
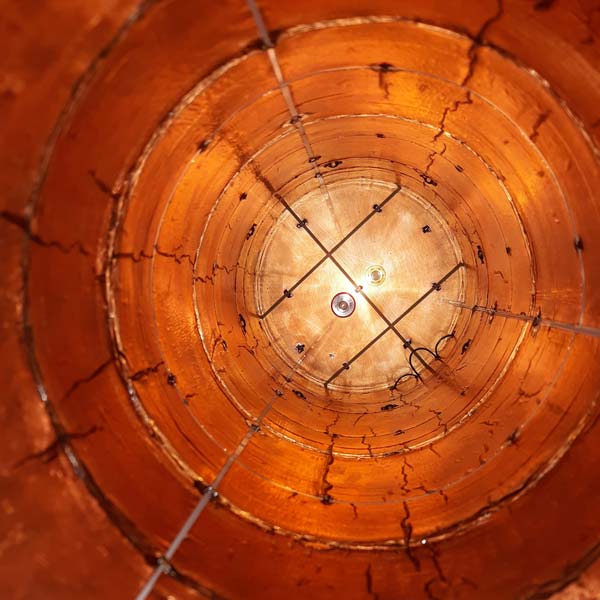
‘Signs of Life’
Around 5:30 p.m. at the low-field lab in Gramercy Park the organizers said they had moderated the evening’s goal from obtaining images to acquiring signal, a precondition for imaging.
“Once you get the signal, you could get an image pretty quickly,” said Dr. Cooley. Doing so in the next 150 minutes was “not completely impossible,” she said.
The scanner was now connected to a computer board known as Red Pitaya—an electronic brain the size of a card deck equipped to rout commands to the hardware and read data received from the scanner. The Red Pitaya lay on a desk next to an open laptop belonging to Sairam Geethanath, PhD, assistant professor of diagnostic, molecular, and interventional radiology at Mount Sinai, who led the scanner-control software team. Dr. Geethanath is among the authors of pypulseq, a software library developed to support India’s national mission to produce a homegrown 1.5 T medical MRI system. The library can control scanners of the major MRI brands that speak different proprietary languages, a capability the community calls “vendor agnostic.”
“I can’t tell you how excited I am about this hackathon,” said Dr. Geethanath. Together with Tobias Block, PhD, leader of the user-interface team, Dr. Geethanath had laid the programming foundation for the acquisition, reconstruction, and interface services, and double-checked that the external libraries they had planned to use could talk to each other. “You need to make sure you don’t break anything when you bring things together,” said Dr. Geethanath.
Throughout the week, the scanner-control and user-interface software teams used dummy data and a tabletop MRI system, originally designed more than a decade ago by Harvard researchers—including Drs. Cooley and Stockmann—for a course at the Massachusetts Institute of Technology. The tabletops have since found educational and research uses in laboratories around the world, including at NYU Langone. At the hackathon, the tabletop stood in for the MRI hardware until enough of the latter was ready to attempt integration.
Bringing things together proved to be the toughest part of the challenge. At one point, the teams used a synthetic signal source to troubleshoot the failure to receive a pulse from the scanner. The MRI—strapped to the cart and connected to an oscilloscope, the blinking Red Pitaya, Dr. Geethanath’s laptop, and tended to by a crowd of people—resembled an intensive-care patient with poor vitals.
Then, the shape of the readout on the oscilloscope changed from square to triangular.
“That’s beautiful,” pronounced Dr. Stockmann. “That’s a gorgeous pulse. You can get tons of signal with that.”
But around 6:00 p.m. the Red Pitaya died, possibly from overheating, and had to be replaced. All around, people were still pursuing projects: mapping the RF coil, assembling the passive shims, checking the fit of the multi-coil shim/RF shield combo, searching for sources of electromagnetic interference, examining cables, debugging the RF transmitter, testing the receive preamps, tweaking the timing of the gating signals, and so on.
As eight o’clock slipped by, the laboratory became quiet.
Asked what just happened, Dr. Stockmann said, “nothing happened—that’s the problem. We’re completely at step zero, trying to get signs of life. … It’s a needle in a haystack until you get that first signal, and it’s always the hardest part.”
Troubleshooting continued, but as the deadline’s urgency faded, the crowd began to diffuse throughout the research suite, which now included a makeshift afterparty room with music, food, and drinks. Some participants kept working on the scanner into the wee hours, but eventually even the most determined had to call it a night.
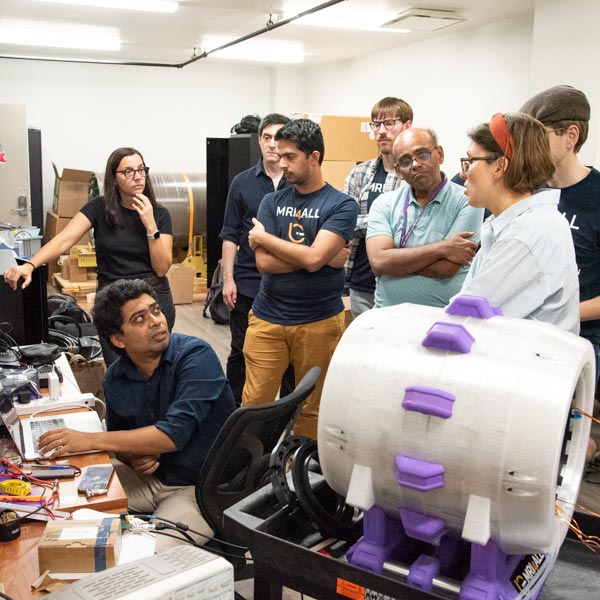
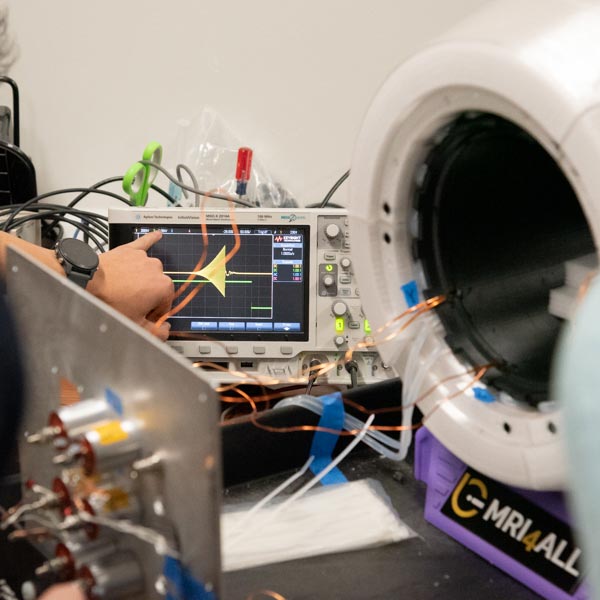
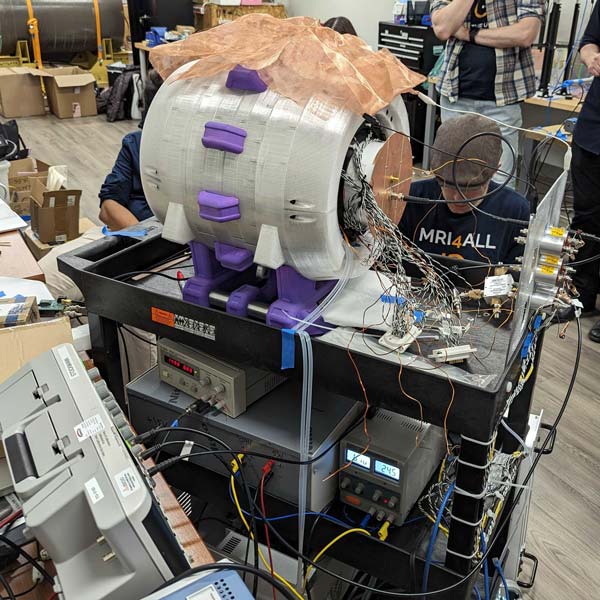
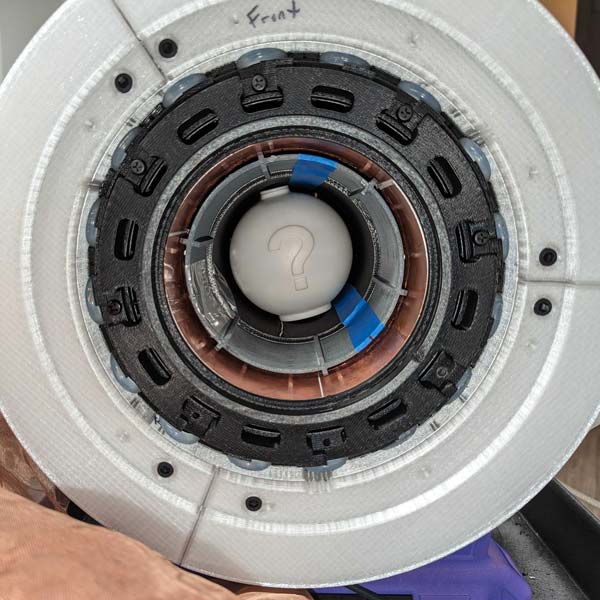
Zeugmatron, What Is It For?
That Saturday night, the hackathon teams had got tantalizingly close to signal, and it wasn’t long before magnetic resonance images began to emerge. After a two-week break, several team leaders returned to the low-field laboratory to take a close look at the whole system and eliminate bugs. One major factor turned out to be environmental in the form electromagnetic noise permeating the building. The interference—not uncommon in a dense city bristling with electrical and electronic equipment—had made the “needle” of signal particularly challenging to find. The researchers solved this by placing the scanner in a shielded room and using a high-quality synthetic power supply. They also fixed some issues with the RF shield and the RF coil, including a loosely soldered joint, which Dr. Stockmann called “a classic.”
“It was fun to see the first pictures,” said Tobias Block, PhD, who co-organized the hackathon and led the user-interface team. The first image, obtained in early November, shows a cross-section of two water-filled syringes and resembles a projection of two “glass capillaries filled with H2O” from a foundational 1973 paper by Paul Lauterbur, MRI’s co-inventor.
The allusion to MRI’s origin is deliberate. Hackathon participants had named their creation Zeugmatron Z1, a reference to “zeugmatography,” the term proposed by Lauterbur in the same paper that contains the cross-hatched image now archetypal to the field. Lauterbur’s coinage didn’t stick, but its etymological root in a Greek term meaning “to join, unite” resonates with the ethos behind today’s growing interest in the potential of low-field, open-source, accessible MRI.
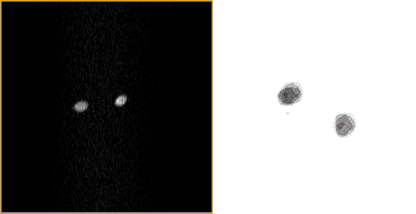
In late November, a Zeugmatron scan of the hackathon phantom revealed another metaphor. In the image, dark letters on a light background spell a message: together is power.
In the context of low-field MRI, “accessibility” often refers to the possibility of bringing simple, affordable, and easily maintained medical imaging devices to communities that do not have the resources to support standard clinical scanners. But in the context of the Zeugmatron, the term means something different.
“It’s more about making the development environment accessible to researchers,” said Dr. Block. “Right now, in order to develop something on an MRI scanner, to run experiments … you need to have a research contract with a vendor, plus you need to have scan time.” The economics of owning, operating, and maintaining MRI machines incentivize imaging clinics to maximize “clinical scan time,” similar to how the economics of air travel push airlines to maximize airplane use. This dynamic can make research scan time scarce.
“So far, there are very few [research] groups who are able to build their own MRI scanner and have a complete development environment,” said Dr. Block. “If other groups are now able to reproduce the [Zeugmatron] platform and build upon that … it could be really interesting because now suddenly students can play around with this, trying new ideas.” Working with an open system makes it possible to develop deep integrations with, say, machine learning algorithms, without encountering the types of barriers present in proprietary scanners.
Dr. Alon voiced a similar vision. “At least that was one of the goals … to create a valid community that can maintain this open-source project and help develop a new generation of devices, maybe more innovative and different,” he said.
An MRI4ALL page on GitHub documents much of the Zeugmatron. Some elements are yet to be shared, but the organizers say their goal is to complete the repository soon.
“By making it open source, we’re providing some guidance and some resources to people really anywhere to be able to replicate, or at least give them a starting place to build something like this,” said Dr. Cooley.
The exercise has already proven valuable even for the experts. “Being able to work on every aspect of the scanner … has taught me a tremendous amount about how MRI works,” said Dr. Stockmann. “When you’re using a high-field scanner, kind of like driving a car, you don’t pay attention to a lot of the stuff under the hood. And when you do low-field, you have to pay attention to all the details … you learn a lot.”
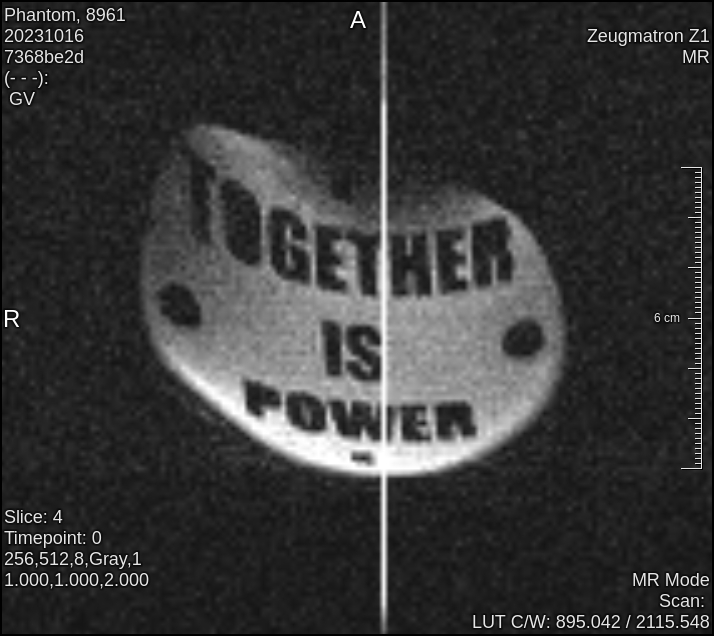
Related Story
In a return from a pandemic hiatus, the i2i Workshop encouraged a broad and varied look at what imaging is and where it's headed.